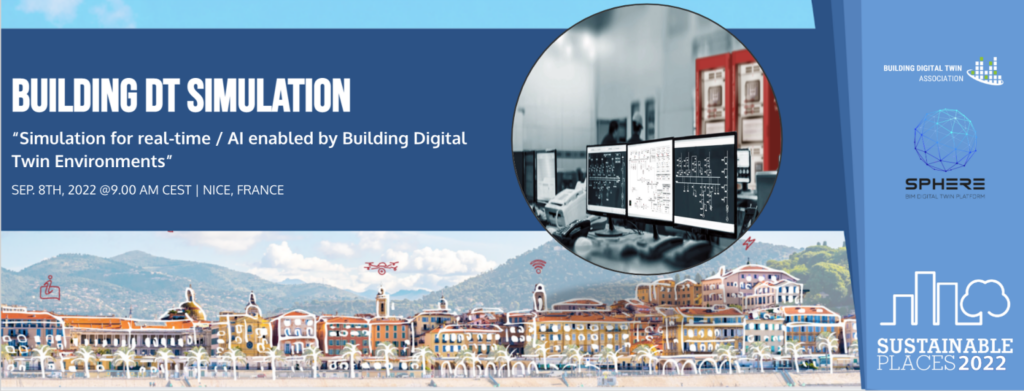
The simulation for energy systems became nowadays a fundamental task that should be carried out during any research or industrial project development. It is not only for system models testing, rather it became an essential phase for planification, optimization and control strategies definition. Additionally, real-time simulation particularly is another targeted milestone due to the big concerns given recently to software, hardware and model-in-the-loop methods. However, energy system complexity and the limitation of hardware resources make it challenging achieving high accurate real-time simulations. Those challenges and others, with the potential solutions, were the discussion subject of the Simulation Workshop in Sustainable Places 2022, held in Nice last 9th September.
SIMBOTS
First, the definition of SIMBOTS, as a simulation platform, is given. SIMBOTS is the mathematical representation of a real machine or equipment based on differential algebraic equations to simulate the real behavior of a system. SIMBOTS can exchange information through inputs and outputs ports that can be of different kinds: fluid, thermal, mechanical, or electrical. The models are generated to optimally perform real-time simulation when implemented into bigger systems and models. Thus, the complexity of the models must be analyzed in detail to reduce simulation times while keeping results as physical as possible. A compromise between computing time and results accuracy must be met. This is meant to achieve far low computing times than real-time while keeping reliable results. SIMBOTS can be imported and exported from different technologies and protocols. Some of them are C++, Functional Mock-Up Interface (FMI), OPC UA, web service and APIs, Excel, Python, Matlab, or any specific software providing a legacy model. A very important point related to the chosen technology is the know-how provided with the component, some technologies could require the equation system to be open and the models are explicitly defined. If that situation is undesired, encrypted or black box options are more suitable.
HARDWARE-IN-THE LOOP (HIL)
As a second topic, the big contribution of hardware-in-the-loop (HIL), in real-time simulation, is discussed. Depending on the real-time degree requirements, which differ between electric and thermal energy systems, HIL and virtual-hardware-in-the-loop (VHIL) have proven their effectiveness in energy system simulation, particularly, for real-time debugging and control strategies testing. One possible option to bring a simulation platform alive is through a SCADA system as it is adopted in Typhoon HIL, in this case, the operator interacts with the HIL hardware via a friendly user interface screen. Additionally, the integration of a third-party software, such as a Python-built test automation software, is possible. The integration of all these concepts in the digital twin is critical for centralizing all the data gathering and models into one single place, and by combining this with the stimulation, one can give digital twins the ability to control a sort of sandbox environment, which helps training operators, testing new control behaviors, etc. One can also allow Artificial Intelligence (AI) and Machines Leaning (ML) being trained using available simulation data or improve real-time troubleshooting capability.
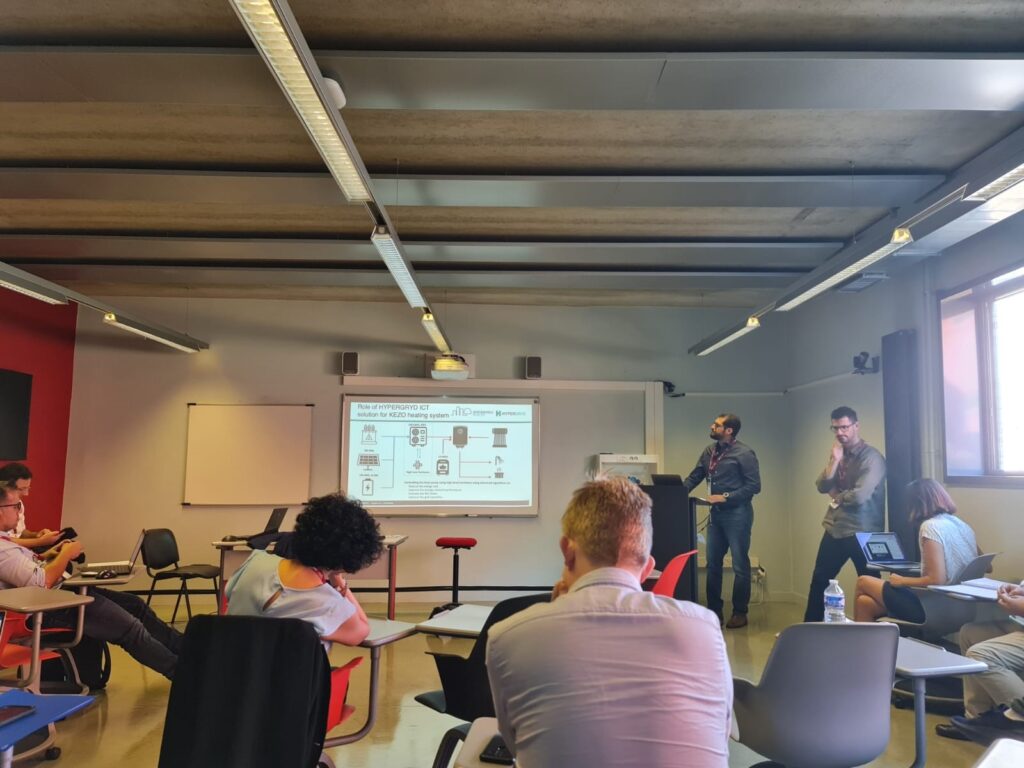
When it comes to higher education, the simulation is a key fundamental skill that engineering students and researchers have to deal with in daily basis. Depending on the education phase (Bachelor, Master or PhD), the simulation tool is imposed by the education program specifications, by an industry-driven problem or according to the research needs. However, many concerns should be taken into consideration when selecting a simulation platform, any simulation software should be capable to load equations inside the controller hardware and solve them independently from the software platform (Modelica, Trnsys, Matlab, etc.). This need is raised recently due to the interests given to the control systems based on the embedded software-in-the-loop solutions. Therefore, the hardware resources should fit with the simulation real-time requirement, particularity for fluid dynamics, which requires usually considerable computing time. Though, as mentioned previously, developers should find a compromise between computing time and simulation accuracy. In the same context, the implementation cost is also to be optimized during the development process.
Regarding HYPERGRYD, the energy system simulation is vital, which is translated to several working tasks. From physical to data-driven models, simulating thermal and electrical-coupled networks in buildings is central to anticipate the system behavior, debugging control strategies and optimize the integration and operation of renewable energy systems (RES). Furthermore, the concept of embedded software-in-the-loop is an active working topic, which is the HYPERGRYD solution tool for heat pumps edge control in a sector coupling application. In this context, KTH is developing and validating a set of software and hardware solutions, that can carry out real-time simulation scenarios in the framework of an optimization-based operation of heat pumps. This task was validated successfully in an experimental setup, while waiting for real implementation on-site in our partner research facility KEZO.
Written by Mustapha Habib from KTH
You can consult the presentations and watch the workshop session: BDT Simulation – Sustainable Places (SP)